Safety
We work to deliver energy responsibly and safely, while looking after our employees, contractors, local communities and the environment. We strive to help improve safety performance throughout the energy industry.
Highlights in 2017
- Following work by a Shell led task force, the International Association of Oil & Gas Producers published recommended practices for addressing safety risks at fabrication sites, which have now been adopted for all Shell projects.
- We recorded the lowest-ever injuries per million working hours – the total recordable case frequency.
- We also achieved the lowest-ever level of injuries that led to time off work, measured as lost time injury frequency.
We work to build a strong safety culture and leadership within Shell. Our Goal Zero ambition is to achieve no harm and no leaks across our operations. To accomplish this, we focus on the three highest-risk areas of safety in our activities: personal, process and transport.
Employees and contractors, wherever they work, must meet our safety standards and requirements, including following our 12 Life-Saving Rules. We strive to reduce risks as far as is technically and financially feasible, and to minimise the potential impact of any incident. These standards also apply to any joint ventures we operate. We work with our contractors to ensure they understand our safety requirements and we help them build skills and expertise to improve their safety performance where needed.
We investigate all incidents and aim to learn from them. Since 2014, around 100,000 employees and contractors have taken part in learning sessions. The sessions focus on how an incident with a potential safety risk could have been prevented and teach participants how to apply the lessons learned in their line of work.
Read more about Shell and safety at www.shell.com/sustainability/safety
Personal safety
Everyone who works for us, or with us, has an important part to play in making Shell a safer place. We aim for a safety culture that goes beyond compliance to one where people feel listened to and cared for and comfortable raising concerns.
We run an annual safety day that gives our employees and contractors the opportunity to learn how they can manage the safety hazards in their work and share ideas with each other. Conversations in 2017 focused on the three themes of care, dilemmas and avoiding becoming complacent about everyday risks.
Process safety
Process safety management is about keeping our hazardous substances in pipes, tanks and vessels so they do not cause harm to people or the environment. It starts with designing and building projects and is implemented throughout the life cycle of these facilities to ensure they are operated safely, well-maintained and regularly inspected.
Read about our process safety performance in 2017.
Process Safety Fundamentals
In 2017, we launched a set of fundamental rules for process safety tasks to enable employees to prevent the release of hazardous materials. These rules help us carry out tasks that are critical for operating safely.
They are based on the process safety operating practices rolled out across our manufacturing business in 2016. By the end of 2017, the number of process safety events related to operational integrity in this business fell by around 30%.
10 process safety fundamentals
Transport safety
Moving large numbers of people, products and equipment by road, rail, sea and air brings safety risks with it. We work closely with specialist contractors and industry bodies to reduce risks.
We have taken proactive steps to improve safety in shipping, for example, working with our global shipping and maritime partners on a programme to improve the quality and consistency of their safety management and on tools to help learn from incidents. In 2017, we carried out around 400 vessel visits to engage mariners on safety and to understand how to implement the programme better in future.
Road traffic accidents claim around 1.25 million lives every year, according to the World Health Organization. Shell employees and contractors drive a combined distance of around 650 million km each year in more than 70 countries. We run road safety programmes, such as our mandatory defensive driving course, which teaches safe techniques and behaviour.
We require everyone driving more than 7,500 km a year on company business and those who drive in high-risk countries to take the in-vehicle defensive driving course. In 2017, 2,900 people completed the course.
Outside our operations, we also work to improve road safety in several communities and countries where we operate.
Our performance indicators report on personal and process safety in line with industry standards. Outside our reporting scope and therefore not reflected in these indicators is a devastating road-tanker incident that occurred in Pakistan in June 2017. A tanker, operated by a contractor, was transporting fuel from the Shell Pakistan Limited oil terminal in Karachi to Vehari when it overturned in the central Punjab province resulting in a fuel spill. Following the accident, people from a nearby village approached the site to collect the fuel spilling from the tanker. Tragically, the fuel ignited and more than 200 people died and more were injured. Shell Pakistan Limited is implementing a long-term relief plan for those impacted.
Read about our transport safety performance.
Road safety in Myanmar
In Myanmar, Shell helped launch a road safety campaign in 2017 to educate drivers and the communities along the Yangon-Naypyidaw highway, a road known for its high accident rate. We ran this in partnership with the Myanmar Red Cross Society and the Global Road Safety Partnership.
The programme also teaches children and adults about safe road use, as many drive motorbikes or are pedestrians along the high-speed expressway. More than 6,000 people participated in the workshops in 11 villages. We also launched a nationwide online awareness campaign.
Road safety in the Permian basin
We have taken proactive steps to improve road safety around the Permian Basin, in Texas, USA, where we have significant shale acreage. Rising oil and gas production activity in recent years has led to increased traffic and more serious accidents and fatalities. In 2015, around 200 people were killed in road accidents in 15 counties, accounting for around 33% of all fatalities reported in Texas.
In June 2015, Shell led the formation of the multi-stakeholder Permian Road Safety Coalition. The coalition has worked to improve road infrastructure and best practice on road safety for oil and gas companies operating in the area. It has also called for funding from local and state governments and and rolled out an annual public education and awareness campaign. In 2016, 118 people were killed in road traffic accidents across the 15 counties.
Emergency preparedness and response
We make sure that we have the necessary resources to deal with spills, leaks, fires and explosions. We regularly test our oil-spill and emergency response procedures and capability to ensure employees and contractors can respond rapidly to an incident.
In 2017, we trained around 2,000 employees in six large-scale exercises to test different response scenarios to potential oil spills at refineries, offshore wells and vessels. All the exercises involve our emergency response contractors and the local authorities. One simulation exercise in The Hague, the Netherlands, for example, focused on a large marine oil spill. Part of the emergency response for the 200 trainees involved mobilising deep-water equipment to cap the leaking well and then collect the oil in a vessel.
During drilling operations, we gather and analyse information about wells to better understand the geology of the area. Pressure and temperature sensors track conditions in real time so that we can immediately detect any changes. Shell-operated drilling activities are monitored from a global network of onshore operating centres which allows oversight and timely technical support.
Internal voice: "We pooled the industry's best technology and ideas to improve well safety"
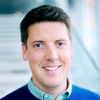
The Subsea Well Response Project is a unique group of nine oil and gas companies that came together following the BP Macondo incident in 2010 to prevent any occurrence of this kind happening again. It has pooled the best technologies, ideas and plans from all the companies involved. In 2017, we saw the culmination of these efforts with the delivery of a new set of containment hardware called Offset Installation Equipment.
One of the challenges we faced was that as a group of nine companies, we were not all aligned on how much effort would be required. We broke the process down into smaller steps, first agreeing to invest in capping stacks, which created time and space to work on the feasibility for a containment solution that could be supported by all the companies. As containment reached its investment decision, we continued working in parallel to mature a solution to cap shallow water wells: the Offset Installation Equipment.
I am very proud of what the project achieved, but there is still a significant responsibility on everyone involved to use this equipment properly to prevent future incidents.
Hurricane Harvey emergency response
In August 2017, Hurricane Harvey forced Shell to safely shut down the Shell Deer Park manufacturing complex, shut in deep water Gulf of Mexico facilities and temporarily close the Houston Lubricants plant. Many pipelines were down or had reduced feeds and several facilities in the region suffered supply issues. It was critical to get Shell facilities safely back online and to supply our customers.
We sent response teams to remote locations to provide much-needed support to staff and residents in the region. Among several other contributions made by Shell and staff, we donated $1 million to the Hurricane Harvey disaster relief fund of the American Red Cross and provided office space for people involved in the response.
Raising industry standards
We share our safety experience and standards with other operators, contractors and professional organisations, including the International Association of Oil & Gas Producers (IOGP).
In 2017, IOGP published recommended practices for addressing safety risks at fabrication sites. Shell led the task force within the IOGP which developed these recommended practices and is now working on a set of enabling activities and a resource library to support their implementation. From June 2017, we adopted recommended practices at all Shell projects.
In 2017, together with several South Korean shipyards, we developed a set of common safety practices that are being implemented at all fabrication yards in the country.
Shell’s Prelude floating liquified natural gas facility and the Appomattox hull, our deep-water development in the Gulf of Mexico, were both built in South Korea.
Appomattox
The Appomattox development is a cornerstone of our global deep-water strategy. The hull was completed and arrived in Texas, USA in 2017. Construction of the host platform and fabrication of undersea infrastructure is now under way and Appomattox is on track for first oil by the end of the decade.
Appomattox is one of Shell’s first major projects to implement construction site safety standards, a predecessor to the IOGP's recommended safety practices for fabrication site construction. These standards are being applied by all of Appomatox’s major fabrication and installation contractors. They address key construction safety hazards such as dropped objects, working at height, lifting and hoisting, and confined space entry. They also provide a framework of activities for health, safety, security and environment leadership, care for the workforce, training, and upfront planning.
Shell will also deploy an advanced well-capping stack for Appomattox, allowing us to quickly shut-down operations in the unlikely event of a spill.
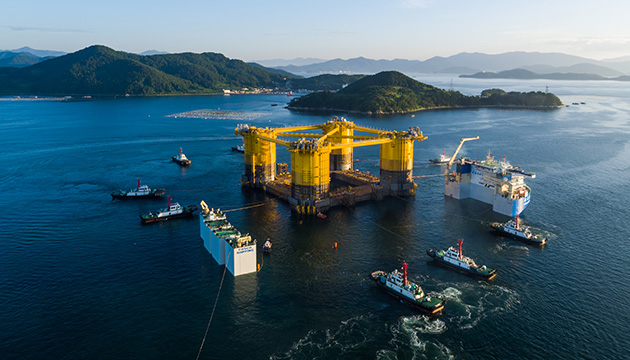
The Appomattox project hull is prepared for its journey from Geoje, South Korea to Ingleside, Texas, USA, to complete the semi-submersible host platform’s construction.
Working with our contractors
We work with our contractors to ensure they understand our safety requirements and together we build skills and expertise to improve safety performance.
Since 2014, executives from Shell have partnered with chief executive officers of major contractor partners to identify strategies and practical steps to improve the safety culture and achieve our Goal Zero ambition of no harm and no leaks, including driving standardisation together. The initiative now includes 18 contracting companies.
Sharing our resilience programme
Resilience is about working through difficult experiences and having the ability to bounce back quickly.
Our contractor partners Subsea 7 and Heerema Marine Contractors, together with four other engineering and construction firms, have developed a series of training videos on resilience for offshore crews based on Shell’s resilience programme. The International Marine Contractors Association is now adopting the approach and making it available to all contractor members from 2018.
Our programme improves not only employee resilience, but employee engagement as well. Shell data show a correlation between engagement and safety performance: a 1% increase in engagement can result in a 4% improvement in safety performance.
Security
Managing security risks is part of our effort to protect our staff, contractors, nearby communities and the environment.
In line with our goal of no harm to people, we carefully assess the security threats and risks to our operations. We work with governments and partners to safeguard our facilities and projects and provide a secure working environment for our employees and contractors. Shell only uses armed security in countries where the threats are most severe, or if it is a requirement under local laws.
Security and Human Rights
We continuously work to maintain the safety, security and human rights of our employees, contract staff, and local communities. The Voluntary Principles on Security and Human Rights (VPSHR) are implemented across Shell operations where there are identified threats of infraction. Shell continues to play an active role in the Voluntary Principles Initiative (VPI), and in 2017 was the chair of the Corporate Pillar, and a member of the steering committee, working with other partners on the initiative to advance security and human rights implementation.
As part of our internal implementation efforts, we include VPHSR clauses in our private security contracts and raise the principles in our engagements with public security forces. We carry out annual risk assessments and develop plans to manage the identified risks. In Tunisia, for example, we trained private security providers on VPSHR and human rights. In Nigeria, we continued to work with a third-party human rights institute to deliver human rights training to our operational teams. For more details on our implementation, please see our VPSHR report(www.shell.com/humanrights).