TOTAL RECORDABLE CASE FREQUENCY (TRCF)
Injuries per million working hours
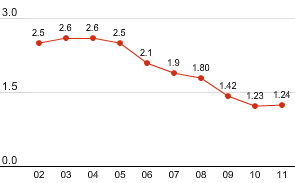
Safety
We continued to make good progress in our safety performance in 2011. We maintained our lowest-ever level of injuries per million working hours, the total recordable case frequency (TRCF). We also maintained our lowest-ever level of injuries that led to time off work in 2011, the lost-time injury frequency (LTIF).
Sadly, however, six people working for Shell lost their lives in 2011. This was six fewer than in 2010. Three were industrial accidents during construction, two were drowning incidents and one was a road transport accident. Our fatal accident rate (FAR) – the number of fatalities per 100 million hours worked – continued to decrease. In 2011, we achieved the lowest FAR that Shell has recorded, around 40% below the rate in 2010.
Maintaining safety requires continuous vigilance. For example, in 2011 the Port Dickson refinery (Shell interest 51%) in Malaysia achieved 10 years without a lost-time injury.
Injuries per million working hours
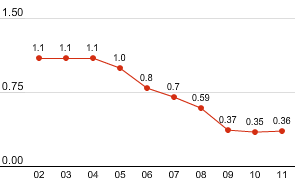
Fatalities per 100 million working hours
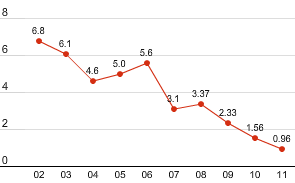
Social investment
We aim to make our social investment projects beneficial to society in measurable ways and to be sustainable beyond Shell’s involvement. In 2011, we spent around $125 million on voluntary social investments worldwide, compared to $121 million in 2010. We estimate that $45 million of our spend in 2011, compared to $61 million in 2010, was in countries that according to the UNDP Human Development Index 2010 have a gross domestic product of less than $15,000 a year per person. In 2011, our social investment increased significantly in countries such as Iraq, Japan and the Netherlands. Our figures do not include investments that are part of contractual agreements with host governments. We also provide significant support through donations of equipment and voluntary work by Shell employees.
Social performance
We continued to implement our company-wide standards for social performance in 2011. They include requirements for the way we engage with neighbours at our major projects and facilities. We have also invested heavily in building the competencies of staff. In 2011, we trained 220 additional social performance specialists in our new requirements. We review annually the extent to which our operations, as well as contractors and suppliers, have processes in place to prevent cases of child or forced labour. We have employee representation in our operations via staff councils or recognised trade unions, in line with local practice.
Local procurement
Wherever possible, we buy goods and services from local businesses. In 2011, we spent a total of over $60 billion on contracting and procurement worldwide. About half of this was spent in Canada, the Netherlands, UK and USA. We estimate almost $12 billion was spent in countries that, according to the UNDP Human Development Index 2010, have a gross domestic product of less than $15,000 a year per person. In these countries, Shell companies spent over 90% of this $12 billion with local companies. We check that our suppliers are complying with key sustainability criteria, including working conditions. In 2011, we conducted 33 rigorous assessments of suppliers in Africa and the Middle East, 120 in the Americas, 268 in Asia-Pacific and 43 in Europe, to assess their compliance in areas such as human rights, labour practices and business integrity.
External voluntary codes
The Shell General Business Principles and Code of Conduct guide the business activities of Shell companies. But we also support a number of external voluntary codes. These include the UN Declaration on Human Rights, the Organisation for Economic Co-operation and Development Guidelines for Multinational Enterprises, and the International Labour Organization Declaration on Fundamental Principles and Rights at Work. In early 2011, Shell joined the new UN Global Compact LEAD programme which strengthens our leadership in the Global Compact and our commitment to its principles.
Diversity and inclusion
Our ability to deliver our business strategy while meeting environmental and social challenges depends on the quality and diversity of our people. We aim to create an inclusive work environment with equal opportunities. We measure diversity and inclusion in part by the representation of women and local nationals in senior leadership positions. By the end of 2011, the proportion of women in senior leadership positions at Shell was 16.6%, up 1.3% from 2010 and up 2.6% from 2009. In 34% of countries where we operate, local nationals filled more than half the senior leadership positions – down 2% from 2010, and down 3% from 2009. In 2011, more than 90% of our employees worldwide were nationals.
Our annual Shell People Survey measures employees’ views of the inclusivity of their workplace. In 2011, 68% felt positive about this, up 2% from 2010 and down 1% from 2009; 12% felt negatively about inclusion in the workplace, down 1% from 2010 and up 1% from 2009.
Training
We continue to invest in the training and development of our employees and joint-venture staff. Our focus is on building technical capability and safety-critical competencies and skills. In 2011, we provided more than 770,000 training days for employees and some of our joint-venture partners. This included training more than 6,000 people in leadership skills. More than 215 senior project engineers completed our externally accredited Project Academy programme that helps to improve the delivery of our major oil and gas projects.
Code of Conduct violations
Shell employees, and contractors working for Shell, must abide by our Code of Conduct. In 2011, 226 violations of the Code of Conduct were reported (205 in 2010; 165 in 2009). As a result, we ended our relationship with 78 employees and contractors (77 in 2010; 126 in 2009).