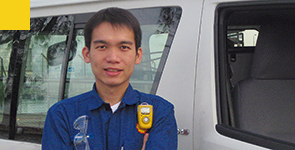
Internal opinion
“The Shell Bukom manufacturing site in Singapore has grown significantly over the last 50 years. Today, there are 1,100 employees and around 3,000 contractors. The site management has a safety programme which included a number of interventions, such as making sure that team leaders had the right skills to promote job safety. A video on Shell’s Life Saving Rules was also produced as part of the induction process.
As a result, despite the increased level of activity in 2013 to 2014, the safety performance on the site improved. In September 2014, Bukom achieved a milestone of two years with no process serious safety incidents at the site. We won a Shell CEO Safety Award in 2014 that recognises this achievement.“ (See “Safety”).
Thomas Wong
HSE and Quality Manager, Bukom, Singapore
When we operate a joint venture, we apply the Shell General Business Principles, the Shell Code of Conduct and Shell standards that cover health, safety, security, environment and social performance. In non-operated joint ventures, we seek to influence our partners to apply materially equivalent principles and standards. We also work with industry partners to share safety standards and knowledge.
Working with suppliers
The building of strong relationships with our contractors and suppliers is essential to delivering our projects and running our operations. When we select our suppliers we look at their commitment and expertise in areas that include innovation, safety, quality and labour rights.
All suppliers and contractors are required to conform to the Shell Supplier Principles. These principles are based on Shell’s General Business Principles. They cover: business integrity such as anti-bribery and corruption; health, safety and environmental (HSE) management; and labour rights. We have a Supplier Qualification System that is used to assess suppliers and identify any potential risk in these areas. This is a service run by an independent company to assess a supplier’s ability to manage its health, safety, ethics and sustainability risks.
Certain areas of our supply chain will pose a higher labour rights risk, based on a combination of their location and the category of goods or services that are being procured. We supplement this with independent analysis to help us identify areas of risk. In 2014, we assessed 1,073 of our suppliers and contractors on their level of compliance with our Supplier Principles.